Common methods to apply the conformal coating materials
There are many methods to apply Conformal Coating. The choice will depend on the following variables:
- Production throughput requirements: The necessary prep work, the speed of the coating process, and how quickly the boards can be handled after the coating process.
- Board design requirements: Connector-laden designs, solvent-sensitive components, and other issues impact your decision.
- Equipment requirements: If a coating is only sporadically required, tying up capital and floor space with additional equipment may not make sense.
- Pre-coating processing: Some processes require masking or taping before coating in order to prevent coating of unwanted surfaces.
- Quality requirements: Mission-critical electronics that require a high degree of repeatability and reliability will generally require more automated application methods.
Common methods to apply Conformal Coating
Manual spraying
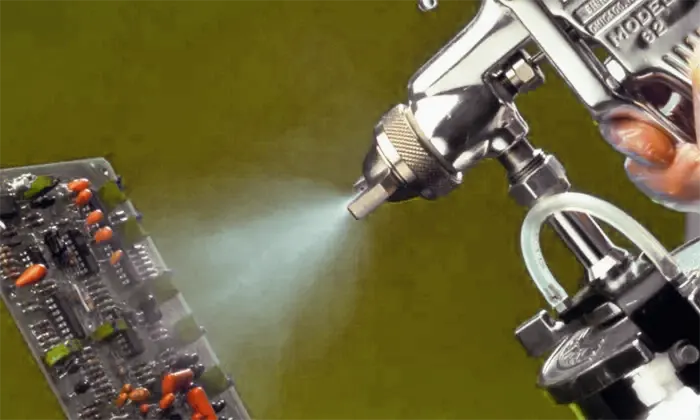
Spraying Gun Conformal Coating Application
When there is insufficient capital equipment for low-volume production, the conformal coating can be administered using an aerosol can or handheld spray gun. However, this method may require masking and can be time-consuming. Additionally, the operator’s skill level affects the quality and consistency of the results, leading to variations between boards.
Full Board Automated Coating System
Programmed spray systems can move PCBs on a conveyor under a reciprocating spray head. Different from Selective Spraying, this method will help to coat full PCB.
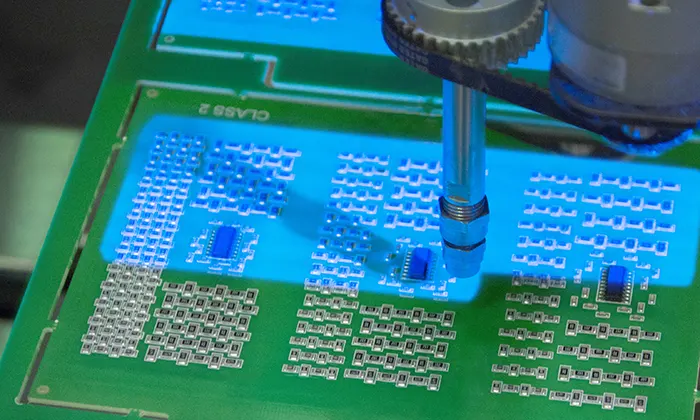
Full board automated coating system zoom in
Selective coating
Employing an automated spray system with a robotic nozzle that applies the coating solely to designated regions on the PCB renders the conformal coating process programmable. This approach is extensively utilized in high-volume assembly, as it circumvents the requirement for laborious masking.
For more information of this Selective Conformal Coating System, please contact Prostech Philippines
Dipping
The conformal coating technique mentioned here is commonly used for mass production. Prior to coating, PCBs typically require masking. Dipping is feasible only if both sides of the board need to be coated. The quality of the film formed is influenced by factors such as immersion speed, withdrawal speed, immersion time, and viscosity.
PCB Dipping in Conformal Coating Process
Brushing
The primary purpose of brushing is for repairing and reworking. Instead of applying a conformal coating to the entire PCB, specific areas are brushed. Although inexpensive, brushing is a laborious and inconsistent technique, making it more suitable for small-scale production.
Vapor Deposition
The method for applying parylene conformal coatings is unique. Parylene undergoes a gaseous transformation when subjected to heat, which is then cooled and introduced into a vacuum chamber where it solidifies into a film and is applied to the entire circuit board. Due to the requirement for specialized equipment and training, outsourcing the process is common.
Different conformal coating methods have their own advantages and disadvantages and are suitable for meeting the specific requirements of diverse coating lines. To learn more about conformal coating techniques and procedures, please get in touch with us for expert advice.