Depending on liquid types, expected productivity and production cost, manufacturers should consider different methods to dispense two-component liquid (adhesive, solder, chemical paste, etc.). To choose the right method for the application, there is necessary to acknowledge the main dispensing systems for Two-part Liquid materials.
In general, there are three types of dispensing solutions to consider: manual dispensing gun, one-component fluid dispenser, and meter-mix & dispensing system.
Manual Two Component Dispensing Gun
Using a dual-cartridge gun is the most economical way to dispense two-component material. Dispensing gun is known as a handheld device and designed in a specific ratio (1:1, 1:2 or 1:10, etc.) and for a specific volume of the cartridge (50ml, 200ml, 400ml, etc.). There are two common operating mechanisms of this gun: pneumatic and cordless.
Pneumatic dispense guns use a controlled, pressurized air source to force fluids out in either lines or dot patterns.
On the other hand, the cordless line of 2K dispense guns offers the most powerful, portable two-component fluid dispensing option. They feature an 18 Volt lithium-ion battery and include intuitive features that make it easy to dispense materials with up to 950 lbs (431 kg) of force for high-volume applications (such as wide joints).
Advantages
- Low-cost dispensing method: no need to set up a costly system, this handheld device provides a flexible and simple solution for low production.
- The easy-to-use plastic cartridges isolate the user from the material, the material is on ratio, and mixing is achieved by a static mixer.
Disadvantages
- Only can apply for low to medium production
- Cannot be used for high precision and small amount liquid application
- Cartridges are one-time use type
- Cannot switch among applications (only one ratio and one cartridge volume)
Automated Dispensing System (Fluid Dispenser)
Fluid Dispensers use air-powered (i.e., pneumatic) mechanisms which help to achieve better precision.
This dispensing method requires pre-mixing part A and part B into homogeneous liquid. At this point, the two-component liquid basically becomes the single component material and is ready to dispense.
The mixture is then dispensed by various methods: feeding into a syringe/ cartridge and then be dispensed by gun/ desktop robot system; or feeding the material directly from large drums.

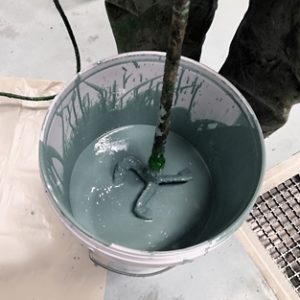
Advantages
- Economical choices: fluid dispenser is a lower-cost system for low to medium productivity compared to the MMD system.
- High precision: This method will make the dispensing process more precise by using a desktop robot or a precise dispensing valve (instead of a manual gun). The accessories for dispensing tasks will help to reduce labor costs, high-quality dispensing results on the finished product or workpieces, and ultimately increase the productivity of the production line.
Disadvantages
Incurring cost for mixture storage: Almost liquid (especially adhesive) must be stored at a temperature of < 5°C, which can create another cost in storage.
Lots of rising issues in the Mixing Stage: mixing is one of the most important tasks when using two-component liquid. This step also includes many possible errors namely:
+ Inaccurate mixing radio: Conducting wrong mixing radio can severely affect curing time, working time, handling time, pot life, and wasting material. For example, if the hardener is poured into the mixture more than the required standard volume in TDS, the curing time will be faster which causes the mixture to be frozen inside the container before using.
+ Air bubble issue: This is a phenomenon happened when air entrapped in the material during manually pouring and mixing two-part process. Large air pockets can cause a ratio imbalance and phasing during dispense, where patches of the adhesive do not fully cure, leaving soft spots and weaker areas. This can often result in costly product failure and rework. You can read more about the negative air bubble issue here.
+ Human-being defects: inconsistency is what manufacturer should worry about when laborers conduct high precision requiring tasks as meter and mixing stages.
Non-optimal System: Fluid Dispenser is not a good choice for mass production. In addition to the problems in Mixing Stage, this semi-automated system will rise many hidden costs (such as waiting time, human labor health issues, quality control, etc.). To optimize mass production in the long term, a fully automated dispensing system will be a better choice.
Automated Meter-mix and Dispensing System
Meter-mix and Dispensing System is currently the fullest system of an automated process for dispensing liquid materials, especially two-component ones. A basic system should contain three different modules: meter-mixing module, motion control module, and dispensing module. This combination can be configured to apply highly filled, highly viscous, and highly reactive materials with high precision.

Meter-mixing module: measure the volume of each part then mix them together. During this process, the materials will be kept in a special container to be dispensed later.
Motion control: After being mixed into a homogeneous liquid, the material will be shipped to the dispensing areas by inside pumps and robots. The robots can be customized according to specific customer demands (depending on budget, working area, and existing process).
Dispensing module: including dispensing valve or dispensing pump system in static or dynamic mixing. The function of this module is to help the materials released with high precision even in the form of dots or lines.
Advantages
- Precise ratio control, improved mixing, little or no wasted material, and limited exposure to toxins.
- Remove air entrapment experienced with hand mixing
- Get risk of all hidden costs brought by a manual or semi-automated process
Disadvantages
- High initial investment cost: This is the bottleneck of almost the automatization process. However, the investment will be worth it if the application is large enough. The cost of the equipment can easily be offset by the reduction in labor and the improvement in quality.
- Exceeding current demand: to be honest, there are cases of unnecessary use MMD. Under the circumstance of an easy-to-handle two-component liquid (low viscosity, low value, and basic mixing ratio), the complicated MMD will be a waste.
The dispensing process is a key step when manufacturers consider using two-part materials. To optimize the whole production line, it is essential to be a partner with an experienced supplier who not only is an expert in automation but also in material. Contact us for further consultation:
Hotline: (+84) 984 695 398
Email: gluexpert@prostech.ph