The primary solids material contained in conformal coatings categorizes into five main types, namely acrylics, polyurethanes (or urethanes), epoxies, silicones, and UV curable.
The selection of a conformal coating is determined by the operating environment of the assembly, as each coating has its own set of strengths and weaknesses. The relative differences between coatings are summarized in the table below, which is also discussed below. It is crucial to acknowledge that evaluations of performance are comparative and not absolute, as they are based on other material types. Moreover, advancements in coating material and polymer technology are constantly diminishing the performance gap between various coatings.
Properties | Acrylic | Urethane | Epoxy | Silicone |
Volume resistivity, ohm/cm (50% RH, 23ºC (73ºF)) | 10^15 | 2 x 10^11 11 x 10^14 | 10^12-10^17 | 2 x 10^15 |
Dielectric constant, 60 cycles | 3-4 | 5.4-7.6 | 3.5-5.0 | 2.7-3.1 |
Dielectric constant, 10³ cycles | 2.5-3.5 | 5.5-7.6 | 3.5-4.5 | – |
Dielectric constant, 10^6 cycles | 2.2-3.2 | 4.2-5.1 | 3.3-4.0 | 2.6-2.7 |
Dissipation (power) factor, 60 cycles | .02-.04 | .015-.048 | .002-2.7 | .007-.001 |
Dissipation (power) factor, 10³ cycles | .02-.04 | .043-.060 | .002-.02 | – |
Dissipation (power) factor, 10^6 cycles | 2.5-3.5 | .05-.07 | .030-.050 | .001-.002 |
Thermal conductivity, 10-4cal /sec/sq.cm/1ºC/CM | 3-6 | 1.7-7.4 | 4-5 | 3.5-7.5 |
Thermal expansion 10-5/ºC | 5-9 | 10-20 | 4.5-6.5 | 6-9 |
Resistance to heat ºC (ºF) continuous | 120 (250) | 120 (250) | 120 (250) | 204 (400) |
Effect of weak acids | None | Slight (dissolve) | None | Little or none |
Effect of weak alkalis | None | Slight (dissolve) | None | Little or none |
Effect of organic solvents | Attacked by: ketones, aromatics & chlorinated solvents | Resists most | Generally resistant | Attacked by some |
@source: Humiseal
Acrylics

Acrylic coatings possess the valuable qualities of rapid curing, fungus resistance, and extended pot life. Additionally, these coatings emit minimal heat during the curing process, thereby avoiding any potential thermal harm to heat-sensitive components. Furthermore, acrylics do not demonstrate shrinkage, which can lead to undue mechanical stress on components and joints.
Acrylics are the most humidity-resistant among the different types of conformal coatings available. Additionally, they exhibit a relatively high dielectric characteristic, fair chemical resistance, and good temperature resistance. During production, they are easy to apply and can be efficiently removed through glycol-based or fluorinated solvents for rework or through direct soldering for spot repairs.
Polyurethanes
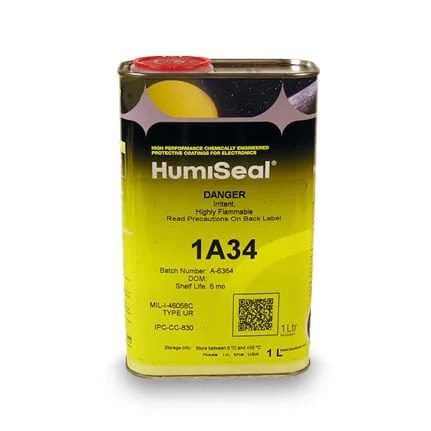
Urethane coatings, also known as polyurethane, possess favorable attributes such as remarkable chemical resistance and satisfactory moisture, temperature, and dielectric properties. Nevertheless, their exceptional chemical resistance can pose a significant disadvantage due to the intricate and expensive rework process required to repair or replace a component. To accomplish this task, a specific stripper compound is necessary. However, the residue left behind by the stripper compound may cause contamination and negatively impact circuit performance and reliability in the long run. Furthermore, if not adequately cleaned, it can hinder the adhesion of the new coating.
Even though polyurethanes can undergo soldering during rework, there is typically a brownish residue that solely impacts the coating’s appearance.
Polyurethanes come in both single and two-component formulations. While single component options are simple to apply, they may take up to 10 days at room temperature to fully cure. In contrast, two-component formulations can achieve optimal properties within 1-3 hours at higher temperatures, but have a pot life ranging from 30 minutes to 3 hours.
Epoxies
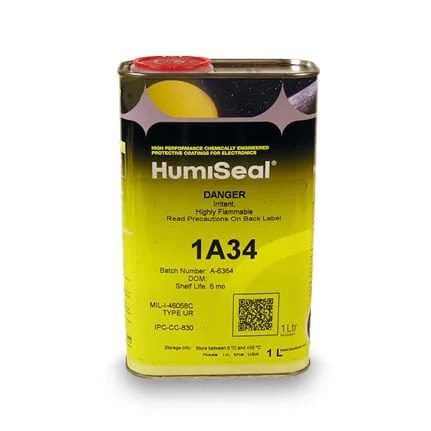
Epoxy coatings exhibit superb resistance against abrasion (i.e. the capacity to endure rubbing) and chemicals, yet exhibit less impressive performance when it comes to moisture and dielectric properties.
Although the cure time is typical, the challenge with epoxies lies in their resistance to removal for rework. This is due to the presence of other epoxy-based materials, such as epoxy glass substrate and epoxy-based plastics in component housings, which can be severely damaged by any epoxy dissolving stripping material. The most efficient method for repairing a board or replacing a component involves burning through the epoxy coating using a hot knife or soldering iron.
What materials are typically utilized as a buffer around delicate components during epoxy application to avoid potential harm caused by film shrinkage during the polymerization process?
Epoxy systems can be cured within 1-3 hours at a higher temperature or within 4-7 days at ambient temperature. The limited Pot Life of these systems imposes a constraint on their practical application.
Typically, epoxy-based coatings come in two-part compounds, although single-component vinyl-modified epoxies are obtainable for specific purposes.
Silicones
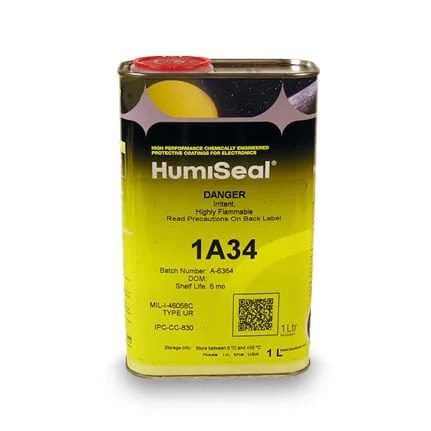
Silicone coatings exhibit exceptional resistance to high temperatures, moisture, and electrical insulators. However, they possess limited chemical durability. Their remarkably low surface tension facilitates their penetration into every component of an assembly. Nevertheless, caution must be exercised to prevent counterproductivity due to their high solids content and Co-efficient of Thermal Expansion (CTE).
Silicone coatings are primarily utilized in high-temperature applications up to a maximum of 200 C, which makes them highly desirable for assemblies that require large heat-dissipating devices such as power resistors. However, similar to epoxies, silicone coatings can be challenging to rework and are relatively expensive when compared to other coating material types. Additionally, silicone materials tend to be 2-3 times more permeable to moisture vapor than other coating chemistries, thus necessitating thicker films for the same level of protection. Furthermore, the CTE of silicones is significant (e.g., 300-350 ppm K) compared to solder (c. 16 ppm K) or other coating types. It is worth noting that silicones possess a unique property where they feel soft under the thumb but are rock-hard when exposed to certain conditions.
UV Curable Coatings
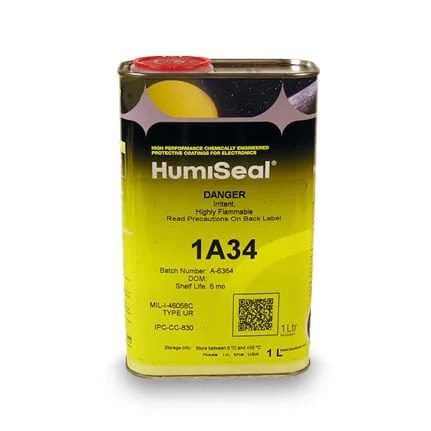
Conformal coatings that can be cured by Ultraviolet (UV) light boast rapid curing, low VOC content, and superior resistance to moisture, temperature, and chemicals. These materials are ideal for selective coating applications with high output and require minimal space for curing equipment, freeing up valuable floor space.
To address shadowing concerns and ensure proper curing of material beneath components that are not exposed to UV light, many commercial formulations include a secondary cure mechanism that can be activated by either heat or moisture. Opting for a moisture-activated cure offers the advantage of avoiding the need for additional process steps. A professional tone is maintained throughout.
UV curable materials possess exceptional chemical resistance, rendering them arduous to rework. However, contemporary formulations can be effectively mended through the utilization of a soldering iron or micro-bead blasting equipment.
Coating Selection Chart
Properties | Acrylic | Urethane | Epoxy | Silicone |
Ease of application | A | B | C | C |
Ease of rework removal (chemically) | A | B | – | C |
Ease of rework removal (burn through with soldering iron for spot rework) | A | B | C | – |
Abrasion resistance (rubbing) | C | B | A | C |
Mechanical strength | C | B | A | B |
Temperature resistance | D | B | D | A |
Humidity resistance (moisture) | A | A | B | A |
Humidity resistance (extended periods) | A | A | C | B |
Pot Life | A | B | D | D |
Optimum cure | A | B | B | C |
Room-temperature cure time | A | B | B | C |
Elevated-temperature cure time | A | B | B | C |
Cost | A | A | A | D |
Property ratings (A-D) are in descending order – A being optimum
Source: Humiseal