Medtech companies that manufacture devices that use small, lightweight tubing may need an alternative to mechanical fasteners to assemble their plastic parts. Their device’s intended use may not allow for gaps produced by ultrasonic welding or fusion bonding, or the cracks that may develop in plastic substrates subjected to solvent welding.
Adhesive technologies can deliver high-strength bonding, sealing, gap-filling, and in-line processing. Although they require time to set and cure, some adhesives can easily bond a variety of dissimilar substrates, as well as seal the bond line.
Some main medical devices requirement and standards for adhesive
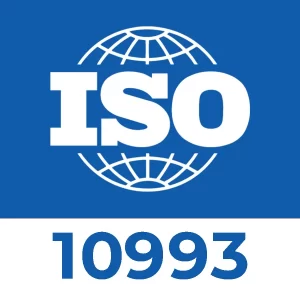
ISO 10993 biocompatibility standards (ISO 10993-5,-10,-11,-4,-6)
Depending on the application requiring an adhesive solution, many of our products also have passed ISO 10993 testing for skin sensitization and irritation as well.
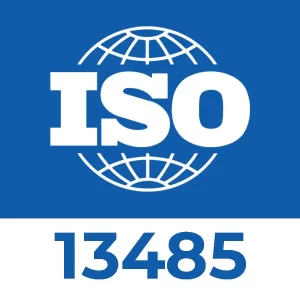
ISO 13485 Medical Devices Quality Management
Ensuring that our products are made consistently and that they will conform to Medical Device Quality Management Standards.
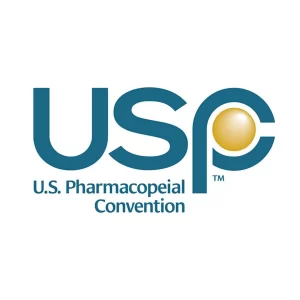
USP Class VI Bio-compatibility of Materials
set by the US Pharma Convention (USP) with a focus on medications, healthcare technologies, food ingredients, and materials used in medical devices.
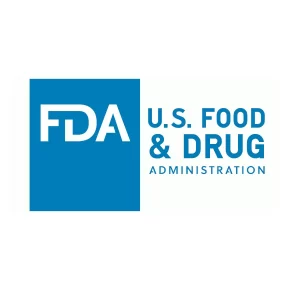
FDA Approval for Medical Devices
Since the user must submit his part for final testing and FDA certification, an adhesive’s qualification to ISO 10993 or USP Class VI is viewed as sufficient to allow a user to determine “probable” device acceptance.
OUR SOLUTIONS
To solve this problem, we are confident to introduce our assembly solution and the one-stop guideline as follows:
Adhesive
The three most commonly used medical grade adhesive chemistries for needle manufacturing are:
- Light Cure Acrylics (both UV cure and LED cure)
- Light Cure Cyanoacrylates
- One-Part Heat Cure Epoxies
Automated Dispensing System for Single Part Adhesive
Though the benefits of fast-setting adhesives, these moisture-cure adhesives can be a challenge, especially when your assembly process requires precise, repeatable dispensing. See details of the Different Dispensing Systems
UV or Heat Curing System
Because UV light of varied spectral output penetrates glass, polypropylene, and many other plastics, both flat and complex 3D-shaped parts are easily bonded instantaneously. By ensuring superior bonding at higher speeds, UV curing produces quality assemblies faster and less expensively. UV Curing System Details here