What is System-in-Package (SiP)?
System in a Package (SIP) pertains to a semiconductor device that integrates various chips, forming an entire electronic system, into one package. Typically, electronic gadgets such as cell phones comprise several ICs, each packaged separately, performing distinct functions such as information processing, data storage, and information exchange. However, with SIP technology, all of these individual chips are combined into a single package, resulting in substantial space reduction and significant downsizing of electronic devices.
Different from SOC (System-on-a-Chip)
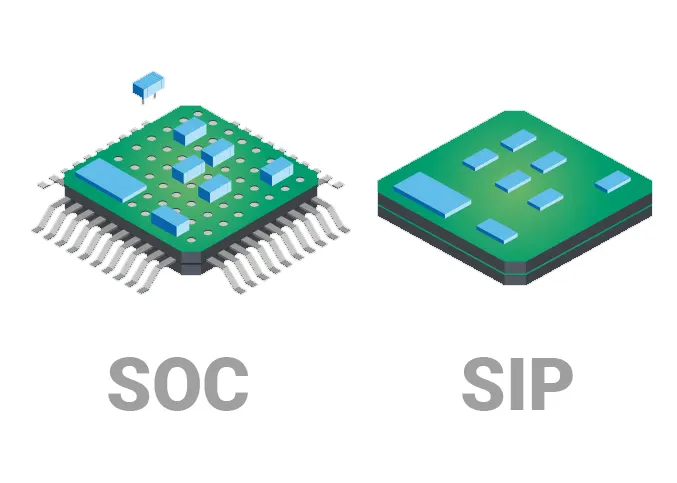
System in a Package (SIP) should not be mistaken for System-on-a-Chip (SOC), which is a fully functional electronic system integrated onto a single chip.
SOC’s are faced with lengthy development periods and expensive development expenses as it is challenging to make diverse circuit blocks function cohesively on one chip.
In contrast, SIP technology merges multiple easily accessible chips into one package.
The updated version of MCM (multichip module)
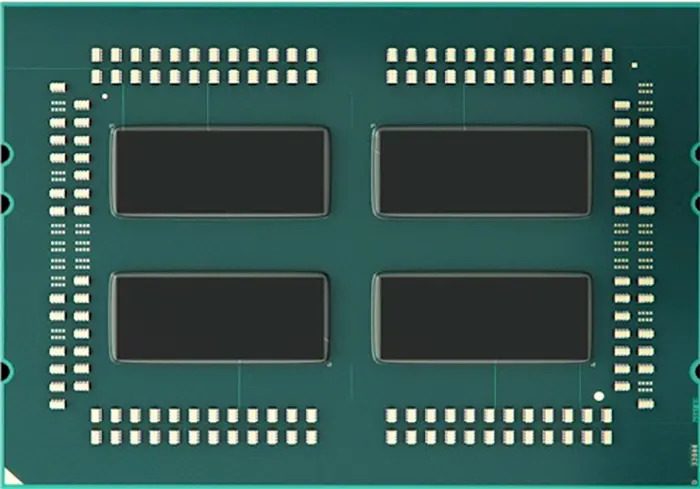
The multichip module (MCM) from the early 1990’s was the predecessor of the SIP. The MCM involved assembling multiple specialized chips in one ceramic package using traditional assembly processes.
Although some people view the SIP and MCM as interchangeable, most recognize the SIP as a separate entity due to its use of advanced assembly technologies and mass-production capabilities
Unlike the MCM, which mounted chips on the same plane, SIP utilizes die stacking as its primary configuration.
Advantages and Disadvantages of SIP
Advantage
- By utilizing existing chips to create a new system in one package, the development time and risk are significantly decreased, allowing for faster product launches.
- SIP technology enables vendors to pack multiple components such as flash devices, SRAMs, DRAMs, microcontrollers, ASICs, DSPs, and passive components into slim packages that can be used in sophisticated electronic devices with sleeker designs.
- SIP manufacturing has several benefits, such as reducing overall assembly and test costs by assembling and testing only one package to create the system.
- Additionally, SIPs achieve better electrical performance due to shorter interconnections. Moreover, they simplify the process of assembling the final application module by requiring simpler PCB layouts, as the complex interconnections are already taken care of within the SIP.
Disadvantage
- SIP manufacturing poses a challenge in the assembly process, as it involves the next-level multi-chip module (MCM) assembly technology. This technology demands the expertise to horizontally assemble and interconnect multiple die placed side by side, as well as vertically stack multiple die on top of each other.
- One of the application of SIP is die stacking, which requires to maintain stability both thermally and mechanically on the substrate. Additionally, interconnections among the dies should be good, while keeping the package as thin as possible. This is the main challenge posed by the die stacking.
- In the development of SIP’s, managing heat dissipation poses a challenge. Simply using off-the-shelf chips in SIP’s can be problematic from a thermal perspective because these chips are designed to dissipate heat through their own packaging. When placed together inside a SIP, heat can accumulate and become a significant issue in real-world applications. Therefore, thermal management is a crucial aspect of any SIP development process.
- The manufacture of SIPs presents difficulties not just in assembly, but also in testing. These systems consist of a range of components, including microelectromechanical systems, optoelectronic devices, sensors, and circuits, all constructed using different wafer fab process technologies and requiring different methods of excitation. Additionally, each individual component necessitates its own specialized testing approach. As a result, creating a test solution that satisfies the diverse requirements of a complex SIP can be a costly endeavor.
The semiconductor industry of the future can reap numerous benefits from the effective execution of SIP manufacturing, such as reduced time-to-market, enhanced flexibility, decreased costs, and smaller size. Nevertheless, achieving this requires a colossal engineering undertaking to tackle all technical challenges that may arise.